Effective decontamination is the cornerstone of safety in the dental practice. Not only must the right equipment be employed, but it must also be used and maintained correctly to ensure optimum results and operational efficiency.
HTM 01-05[i] and SHTM 01-05[ii] provide a baseline for the types of equipment required and the associated testing, servicing and validation of each. They outline general maintenance guidance and mandate the validation of specific equipment.
However, these are not the only documents that must be adhered to for compliant decontamination in dental practices. All must also comply with the Pressure Systems Safety Regulations 2000 (PSSR),[iii] which are applicable to any piece of equipment in any industry that contains a pressure system.
What are the PSSR?
The Pressure Systems Safety Regulations (PSSR) 2000 demand that all equipment incorporating pressure systems must undergo annual testing and certification to ensure their safety. This includes any systems ‘compromising of one or more pressure vessels of rigid construction, like autoclaves’. Dental practice owners are responsible for keeping all the machines in their practices in good condition, protecting both patients and staff from the potential hazards associated with faulty equipment.
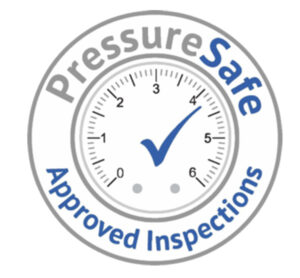
To comply, owners must arrange for equipment testing by a qualified professional who is sufficiently skilled specifically in evaluating pressure systems. Often an equipment engineer, this individual will determine whether the autoclave is safe for ongoing use and has a Written Scheme and a valid signed Report of Examination. These documents must be stored as evidence of PSSR compliance, detailing the specific parts of the pressure system inspected, their condition and any necessary repairs or modifications that were made.
The Written Scheme and Report of Examination is a requirement as part of the annual validation of every autoclave. It is a legality for both practice compliance and insurance.
So, it’s the same as servicing?
Compliance with PSSR is necessitated as part of the annual validation of autoclaves. This is different from servicing. An annual service is a check of the machine to ensure it is in good working order and is fit for use from a mechanical and electrical perspective. Software upgrades as well as minor repairs can be conducted to prevent the development of any major issues later down the line. Though not a legal requirement, regular servicing will keep the autoclave operating correctly, optimising workflow efficiency and reducing the risk of malfunctions, breakdowns and the associated surgery downtime – saving the practice time and money in the long-run.
PSSR compliance follows a formal process whereby a specifically trained engineer has evaluated the equipment and certified it safe for continued use. Non-compliance with PSSR can lead to significant safety risks for patients and staff, with substantial further consequences for the practice. Regulatory authorities can impose a range of financial penalties, with further actions possible should an accident or injury have occurred among patients or staff as a result of practice negligence in this area.
Achieving PSSR compliance
With just a few simple steps, every dental practice can ensure their compliance with PSSR:
- Understand your responsibilities by familiarising yourself with the regulations and how they apply to your practice.
- Safely store your Written Scheme and Report of Examination to demonstrate your compliance.
- Organise annual inspections and certification with a specifically-trained engineer.
- Train your whole team to safely and competently use, test and maintain your decontamination equipment.
All of the above can be more easily achieved by working with a trusted provider of high-quality decontamination equipment, servicing and support. Not only does this afford confidence that the equipment itself will function effectively for maximum safety standards, but it also provides access to ongoing advice and guidance from experts.
Eschmann is renowned across the UK for delivering exceptional service, with its equipment built for efficiency and longevity. The Care & Cover servicing and maintenance plan includes unlimited breakdown cover, Annual Validation and PSSR Certification by a trusted Eschmann engineer, unlimited original manufacturer parts and enhanced CPD user training upon installation for the dental team. There is also comprehensive support available through a dedicated telephone line and from a nationwide team of 50+ Eschmann-trained engineers.
The safe side of the law
Adherence to PSSR is a legal requirement for all dental practices with an autoclave. It is in place to protect both patients and staff from harm. Make sure you’re compliant for the year ahead.

For details on the industry-leading decontamination equipment and unparalleled support available from Eschmann, including equipment validation and servicing, contact the team today at www.eschmann.co.uk or by calling 01903 753322
[i] Health Technical Memorandum 01-05: Decontamination in primary care dental practices. Department of Health. 2023. https://www.england.nhs.uk/wp-content/uploads/2021/05/HTM_01-05_2013.pdf [Accessed January 2025]
[ii] Cleaning of Dental Instruments Dental Clinical Guidance Second Edition Scottish Dental Clinical Effectiveness Programme SDCEP. (2014). [Accessed January 2025]
[iii] Ligisation.gov.uk. The Pressure Systems Safety Regulations 2000. UK Statutory Instruments. No. 128. https://www.legislation.gov.uk/uksi/2000/128/contents/made [Accessed January 2025]